How about bulk hardcover repair? Look at the late-night summary of the front-line project manager, and you’re more confident about doing a good job
In order to improve the quality of decoration projects in an all-around way, effectively carry out cost control, standardize the refined decoration management process, reduce the rate of repair, improve the competitiveness of the company’s products, we must strengthen the hardcover repair project management and control points.
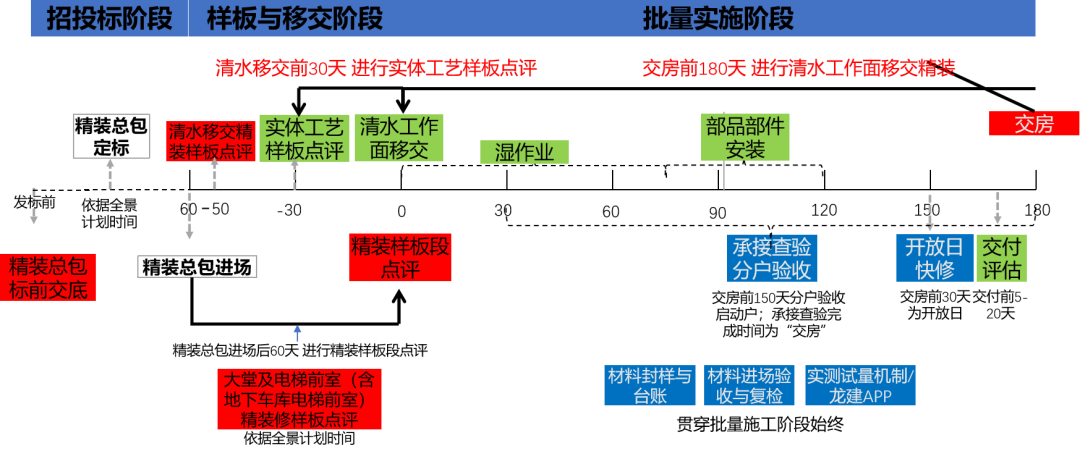
The general idea is
– 5 key nodes in the project control process –
01
Summary of the heavy difficulty analysis
1.1
Difficult analysis
Anti-cracking measures for walls:
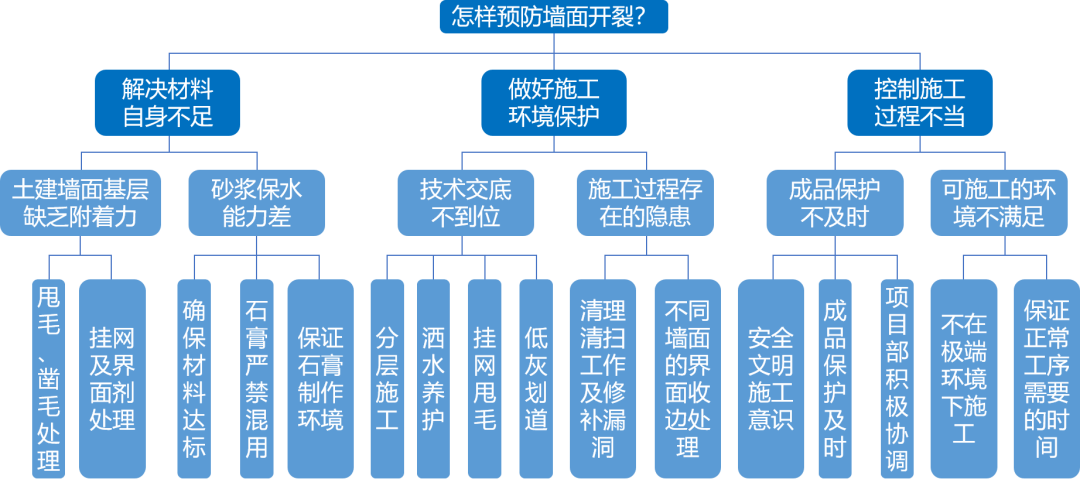
Anti-aircraft drum:
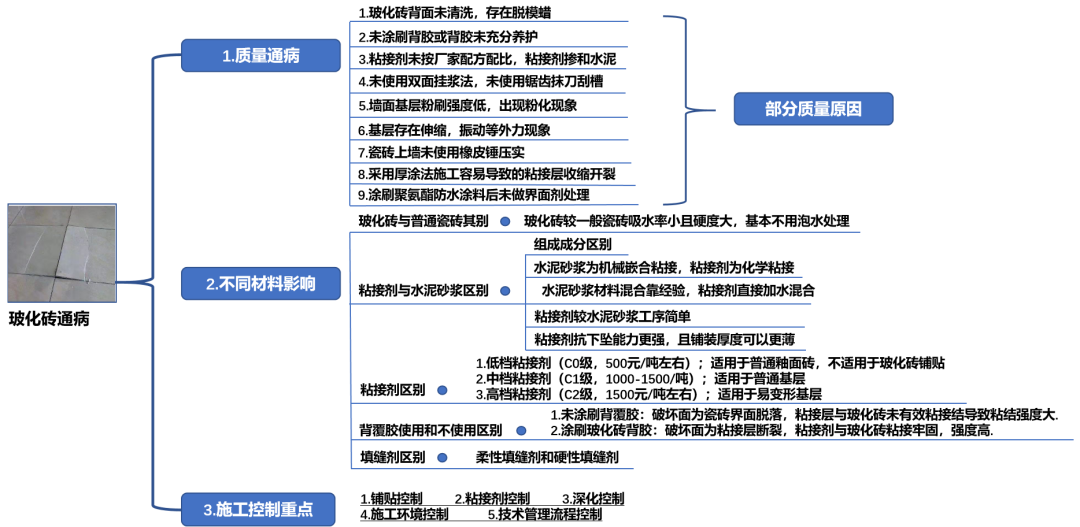
(1) Before the construction, check the original wall for empty drums, shedding and other hidden dangers must not blindly start work;
(2) To prevent the glass brick empty drum and shedding, the glass brick before the paving of its full back glue treatment, so the back glue process is particularly important, focus on inspection (inspection focus: back glue to the edge uniform not exposed bottom), construction using special tile adhesive construction.
Floor tile paving process requirements:
(1) Kitchen and bathroom floor elevation and indoor elevation must meet the design requirements, and the ground should be cleaned.
(2) Tile pattern is consistent, with no scratches, color differences, cracks, pollution, missing angle, and other phenomena.
(3) Before laying the tiles, the drawing must be deeply typographed to determine the loss.

Leak-proof:
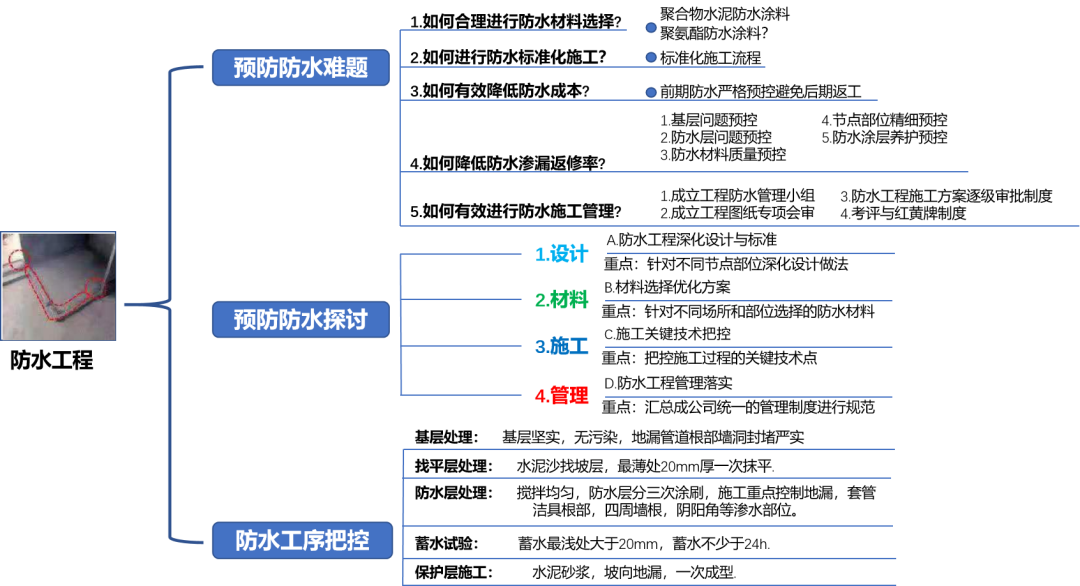
Waterproofing process requirements:
(1) Grassroots clean-up; floating dust, mud blocks, impurities around pipe walls, etc.
(2) The angle needs to be done after arc treatment, water does not leak to block.
(3) New and old walls sewn wire mesh.
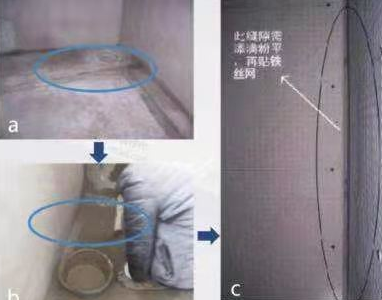
Waterproof control point:
(1) The threshold is waterproof with a water-stopping band brush, waterproofing should be brushed to the dry area (walkway) and turned up 30mm.
(2) The ground leakage position is treated as a funnel.
(3) Shower room water belt.
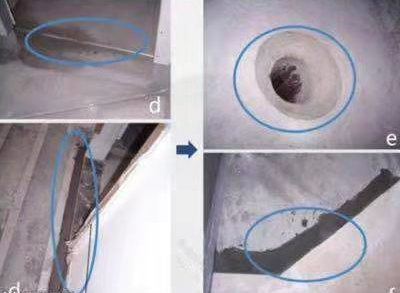
02
Cost control
2.1
Cost management
Develop a project control dynamic table:
(1) The lack of understanding of the process led to measurement errors, this work must have construction staff, budget staff, with shifts combined with the base drawings to participate in the calculation, and let the class sign confirmation.
(2) In the process, the budgeter and the construction staff should check, check and adjust the number of early warning lines in time for the site practice.
(3) For the characteristics of household type unified, batch operation, the basic materials need to be fixed-scale processing, reduce loss, but pay attention to the bottom and unified ingredients, inspection, avoid long cut into short, short throw away phenomenon.
Warehouse management: before entering the project, we need to check the project location (busy areas, suburban areas, surrounding facilities, etc.), affecting the transportation of materials, personnel accommodation, etc.
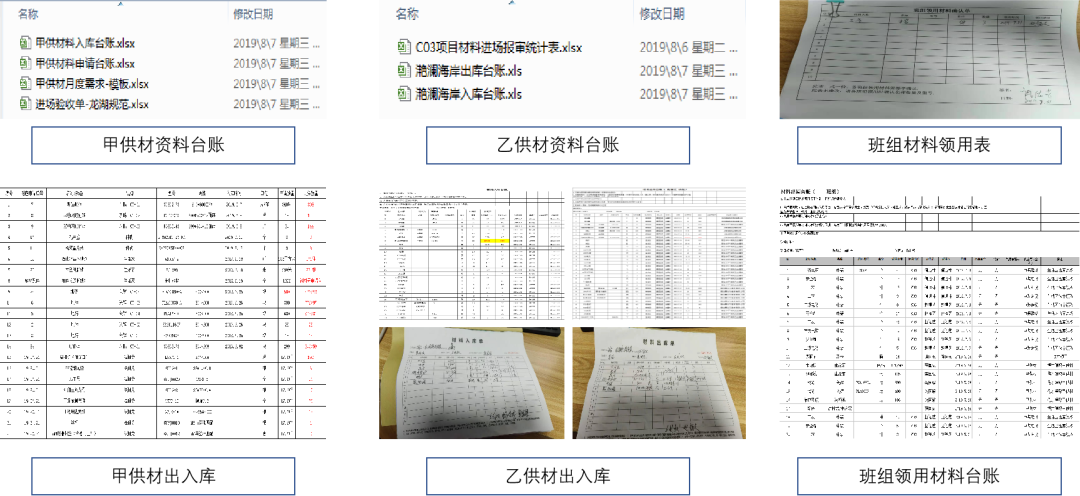
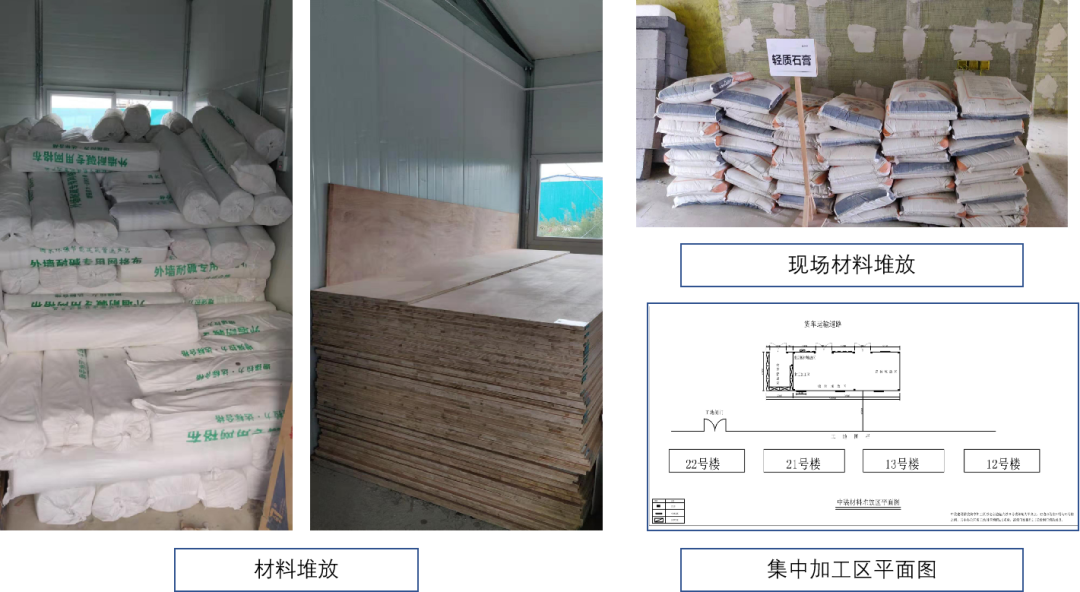
Materials procurement:
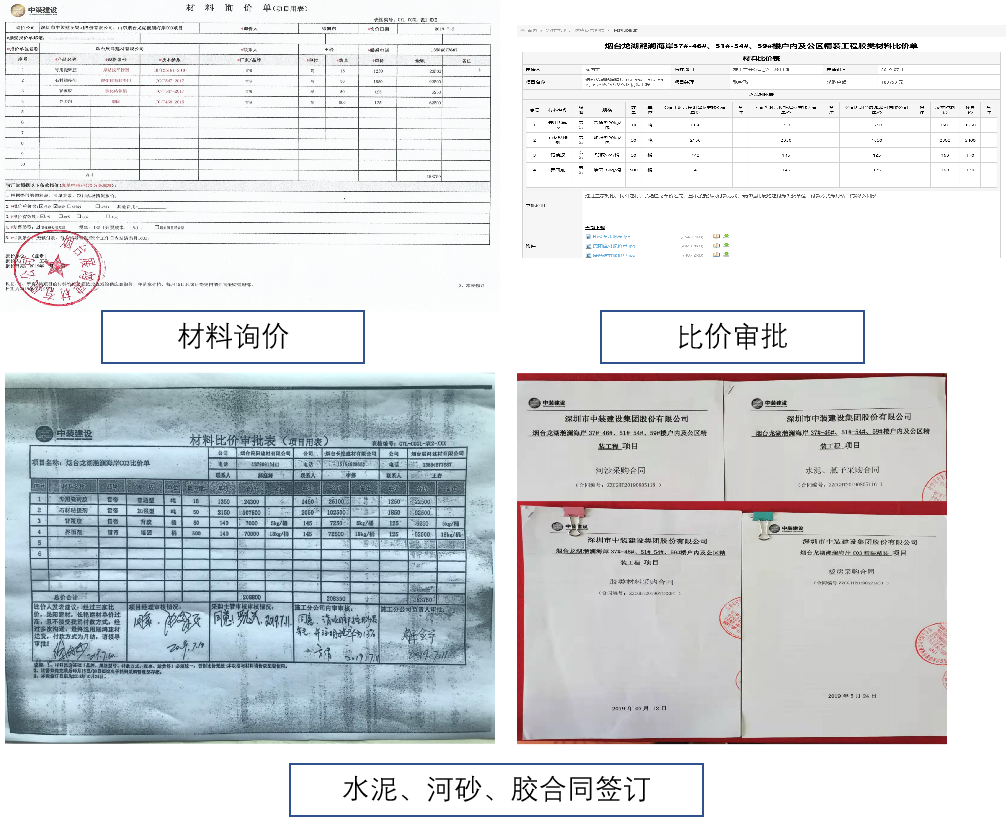
03
Summary of progress
3.1
The total schedule
Keyline determination:
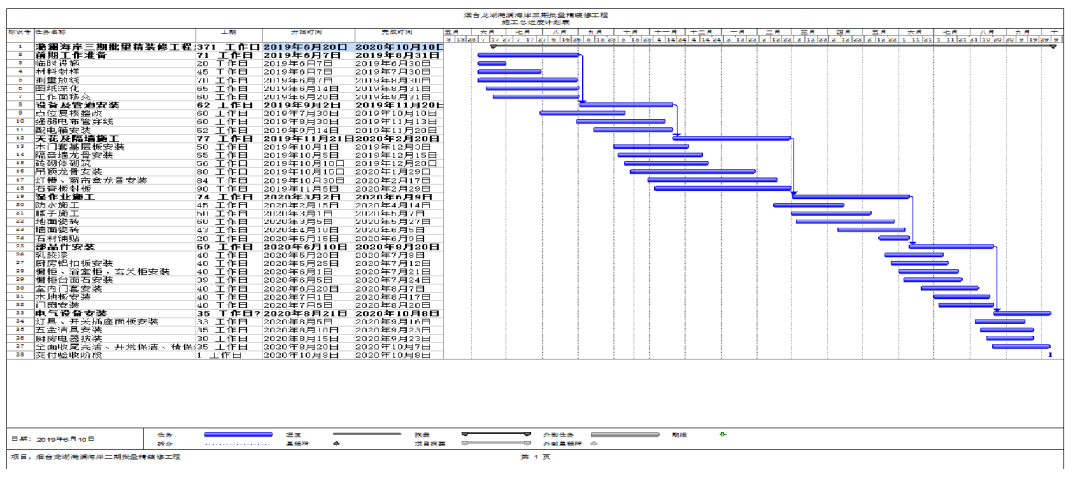
Total schedule
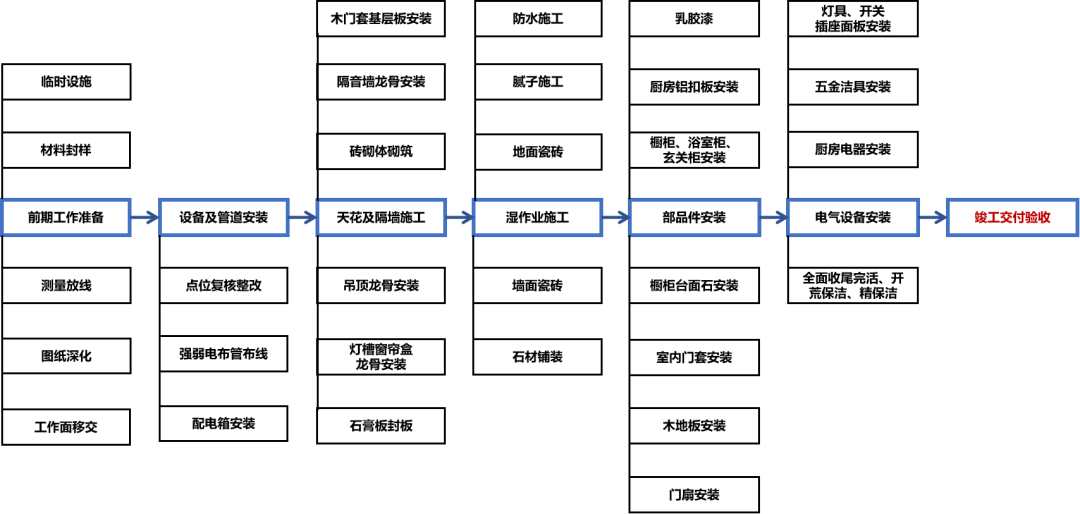
Keyline analysis and control
Keyline analysis (bathroom for example): Before entering the project, we need to examine the project location (busy area, suburban area, surrounding facilities, etc.), affecting the transportation of materials, personnel accommodation, etc.
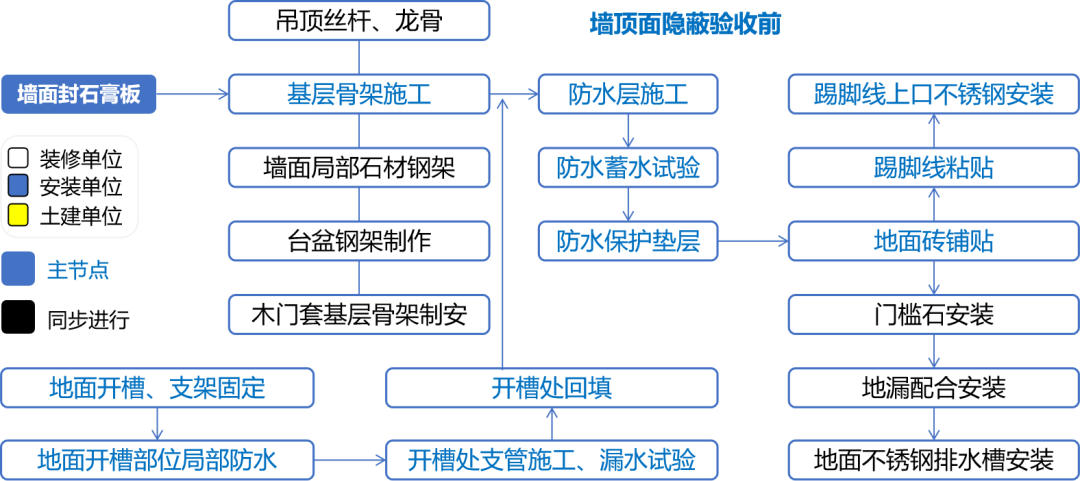
3.2
Progress control
Logical planning:
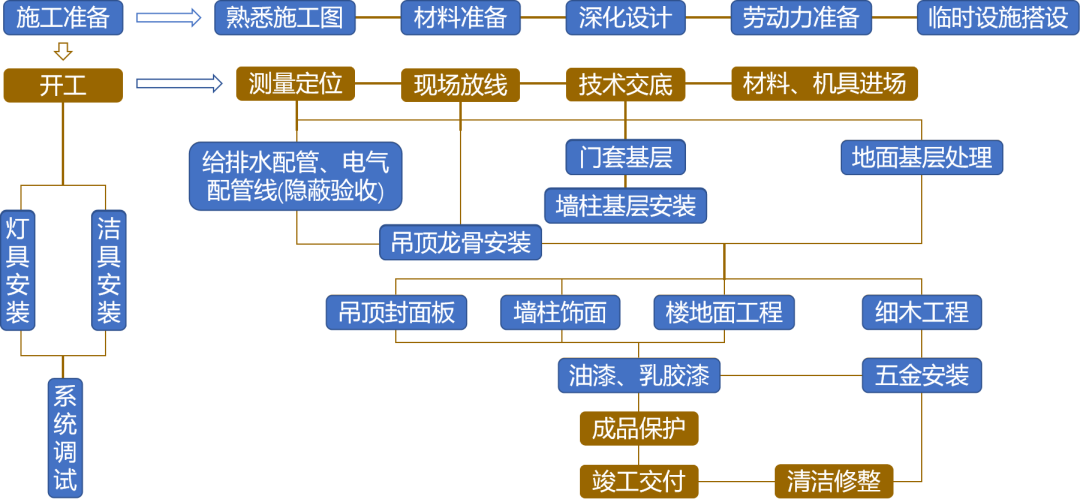
Construction planning:
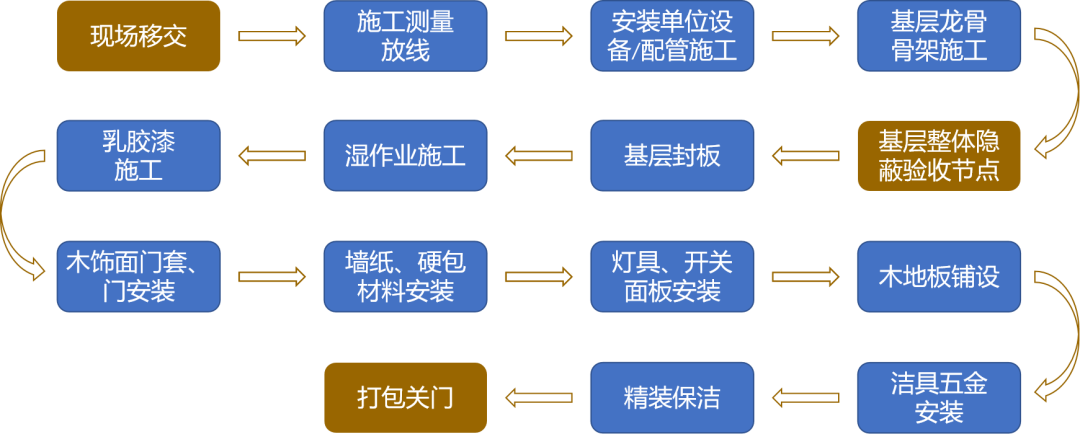
Related schedule:
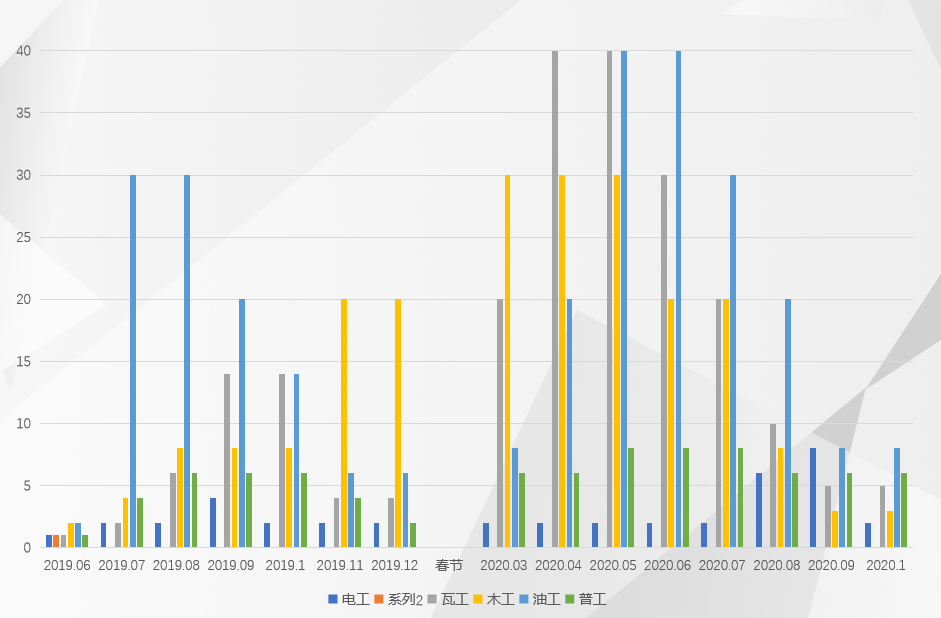
Labor Plan
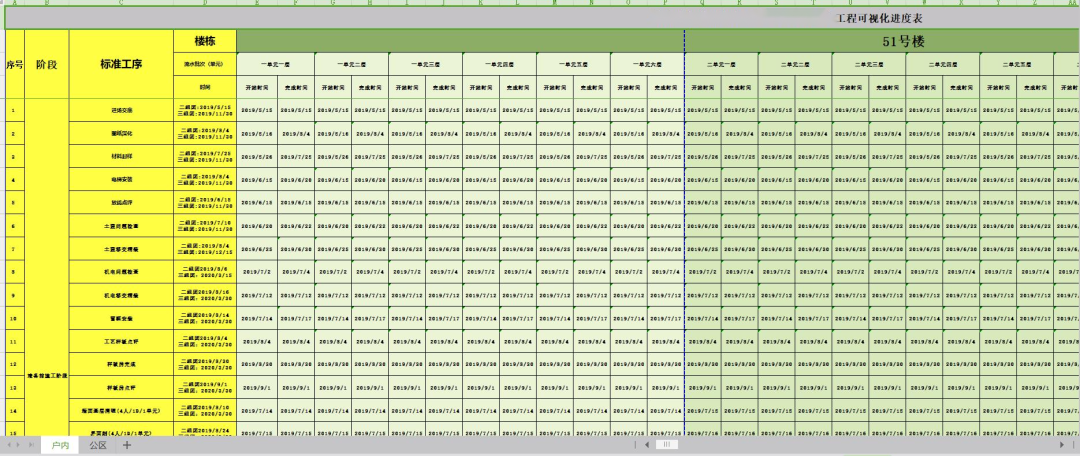
Visual progress control
04
quality control
4.1
Gypsum board ceiling
Process requirements:
(1) The gypsum plate corner seal must cut L-type, and the width of the first layer of gypsum board on both sides is not less than 600mm, and the width between the two sides of the second layer of gypsum board is not less than 1000mm.
(2) The edge of the plate shall not be seriously damaged, the cutting surface is rough and unrepaired;
(3) Light steel keel and gypsum board in the centralized processing area unified cutting processing, the site is not allowed to cut and secondary deep processing.
(4) The spacing of the boom < 900mm,300mm from < the wall edge, 1000mm from the main keel spacing < 300mm from the wall edge, < and 400mmfrom the < of the secondary keel, 200mm from thewall<. The first gypsum board screw spacing < 600mm, the second layer gypsum board screw spacing < 200mm.
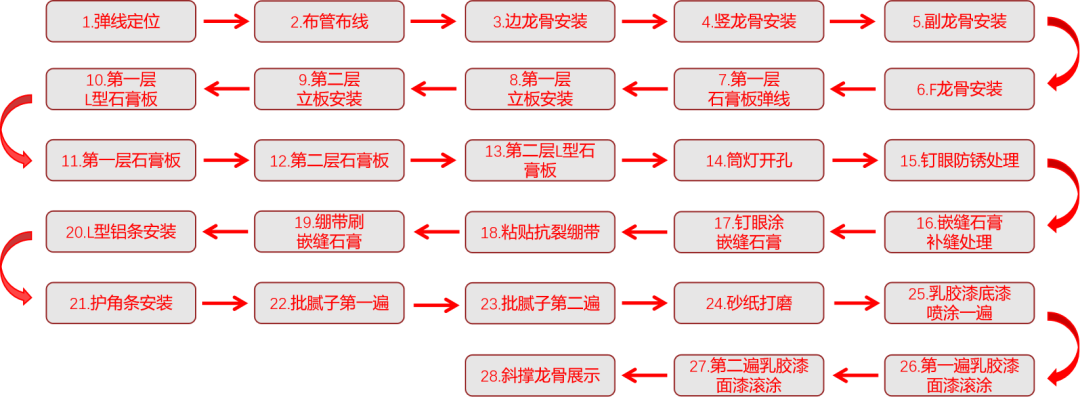
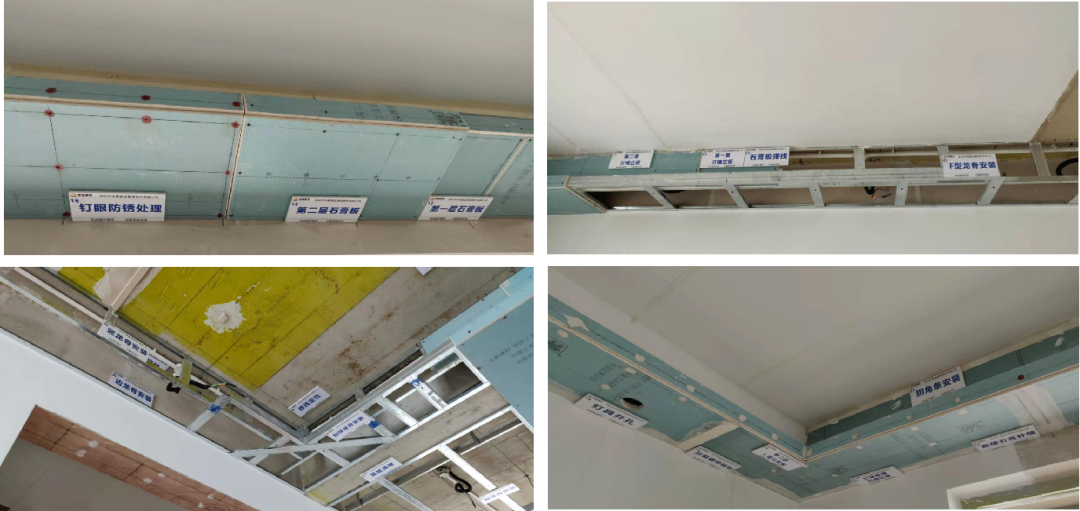
4.2
Wall tiles are laid
Process requirements:
(1) Wall tiles should be laid before the deepening layout, the formation of layout to determine the tile loss rate.
(2) Wet paste higher than 1200mm should increase the hanging net to prevent shedding, tiles should be soaked completely before the placement.
(3) When wet on a concrete wall or a concrete slab wall, cement glue should be used to pull the wall.
(4) Yin and yang angle tile must control the verticality of yin and yang angle and yin and yang angle brick seam size is consistent.
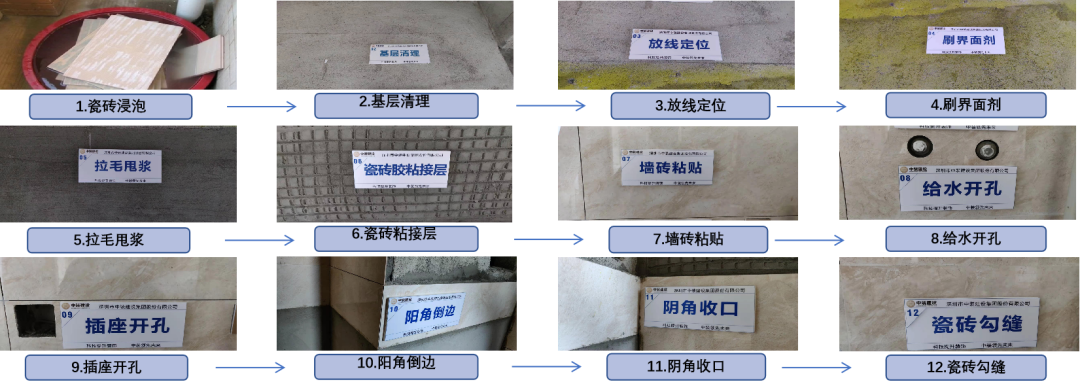
4.3
Wall flour brush plaster
Process requirements:
(1) The and yang joints should be sewn with plaster and should be used with corner guard strips and bandage paper.
(2) When the plaster is greater than 35mm, it needs to be layered with a steel mesh or glass fiber mesh reinforcement to prevent cracking.
(3) Grass-roots gypsum on the wall, different materials between the hanging net (glass fiber net) reinforcement, and up and down the connection width of not less than 100mm.
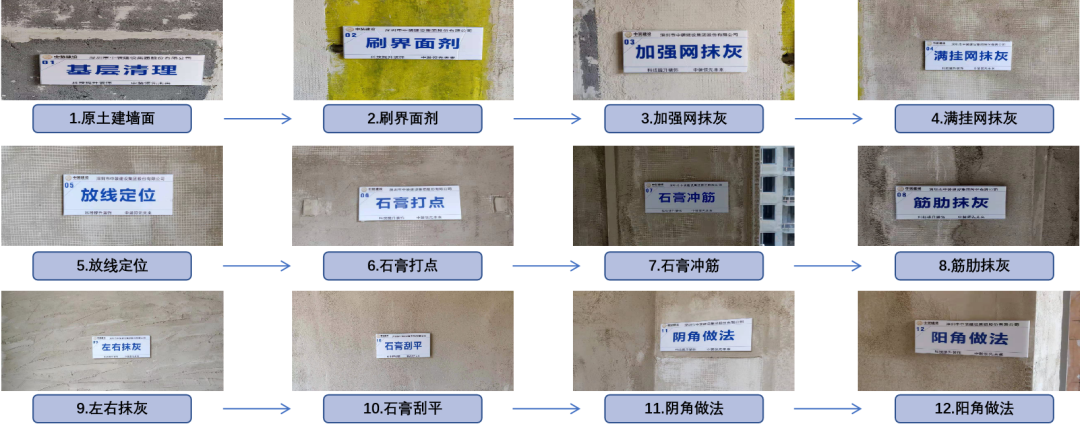
4.4
The ground is flattened
Process requirements:
(1) There shall be no contamination on the ground, cracks, peeling, hemp surface, and sanding.
(2) Ground leakage and slope requirements of the ground, the slope does not meet the design requirements, the emergence of flooding, leakage, water accumulation.
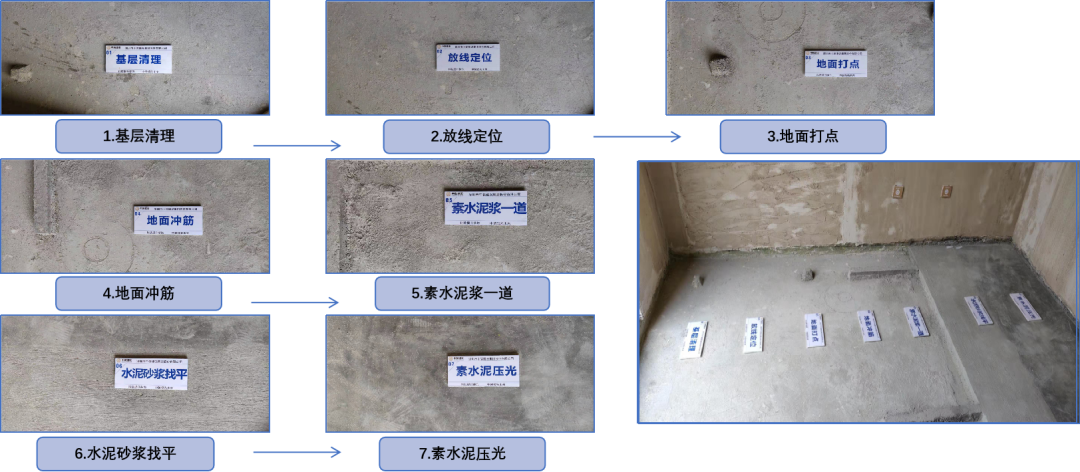
4.5
Wooden floor mounting
Process requirements:
(1) Before laying, check to find the leveling height and ground leveling to meet the requirements, and the ground should be cleaned.
(2) The length of a single wall ≥ 3 meters, should be a whole kickboard, not short stitching, and the kickline is not dust-proof.
(3) Wood flooring should be laid according to separation 3-6-9 and should be reserved around 8-10mm telescopic gap, not short plate straight spelling.
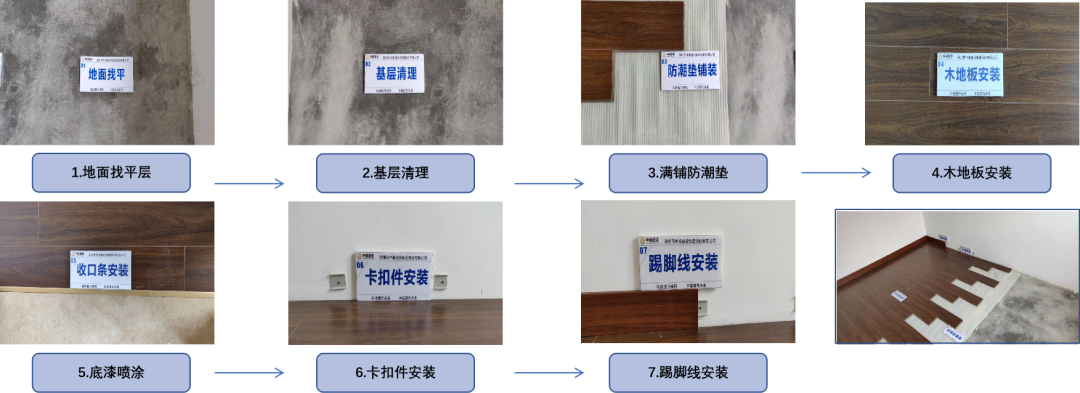
4.6
Tiles are laid
Process requirements:
(1) Kitchen and bathroom floor elevation and indoor elevation must meet the design requirements, and the ground should be cleaned.
(2) Tile pattern is consistent, with no scratches, color differences, cracks, pollution, missing angle, and other phenomena.
(3) Before laying the tiles, the drawing must be deeply typographed to determine the loss.

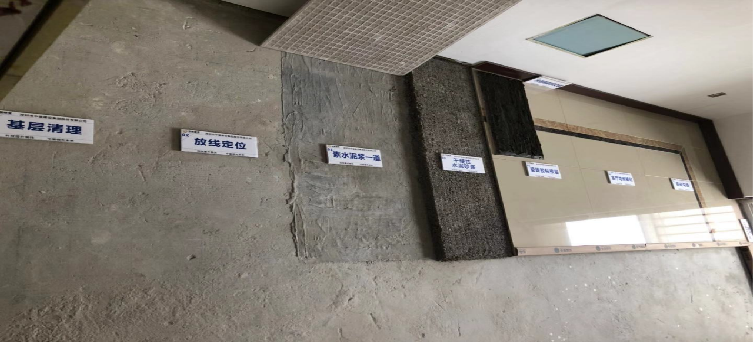
4.7
Window sill slabs are laid out
Process requirements:
(1) The window sill stone is surrounded by tight seams with the wall, and the lower mouth of the stone is tight and flat with the wall seams.
(2) Wet stickers shall not appear empty drum phenomenon, there shall be no scratches, color difference, pollution, deformation, warping, anti-alkali, bumps, cracks, and other phenomena.
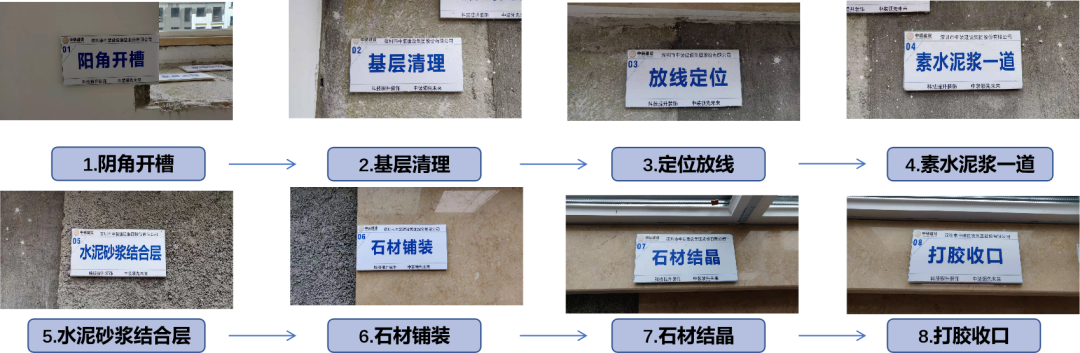
4.8
Aluminum buckle plate ceiling
Process requirements:
(1) The material, variety, specification, pattern, and color of the finished material shall meet the design requirements.
(2) The flatness of the plate surface can not exist bumps, there is a gap between the plate and the plate, and there are high and low displacement and misalignment, and other problems.
(3) The plate surface shall not be less than 1/3 ≥ of the whole plate, placed on the yin side;
(4) When installing an aluminum plate, it must be installed uniformly in the direction of the aluminum buckle plate pattern.
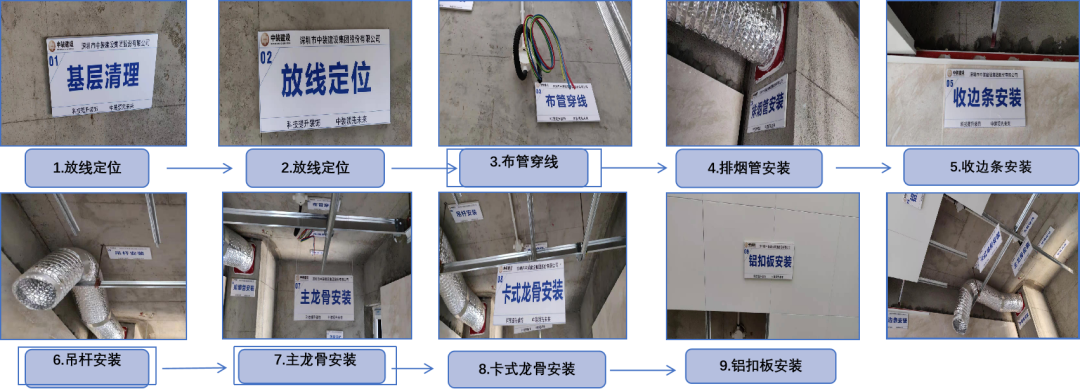
4.9
Electrical installation
Note:
(1) The specifications and models of electrical appliances and electrical materials shall comply with the requirements of the design and the current national electrical product standards;
(2) Lamp specifications, models in line with design requirements, should have a brand, logo, instructions, warranty, etc. ;
(3) The use of PVC wire pipe instead of galvanized steel pipe is strictly prohibited in ceiling, the headline of the ceiling lamp needs to be protected by metal hoses, the length does not exceed 1.2m;
(4) The terminal box used in the communication system, the terminal box and the switch of the power distribution system, the socket should be selected with the same series of products;
(5) After the distribution box household table should be according to the different power of indoor electrical equipment is allocated to power supply, high-power household equipment should be independent wiring installation socket.
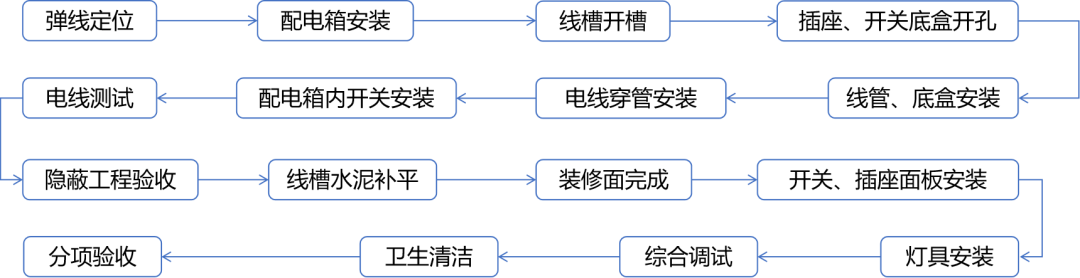
05
Security management
5.1
Finished product protection
Elevator protection: . .
(1) Elevator threshold with 15mm carpentry board square box, to protect the elevator car bottom sill, the use of carpentry board / nine percent board will be the elevator car box wall, floor, top surface protection, set small flip board. After the handover, a professional elevator driver is equipped with a walkie-talkie. Non-professionals are not allowed to build elevators, elevator drivers at any time every day on the elevator car, floor, and elevator car door grooves to clean up, to maintain the elevator car clean and normal use.
(2) Floor tiles: protect at any time after completion. The ground is covered with a finished protective film.
(3) Tile yang angle: the use of a special corner guard strip in the middle, 1.2 meters above the ground for protection.
(4) Wall: Complete the putty before it is finished, finish it, finish it two or three times before the hardcover delivery, polishing, and lacquering.
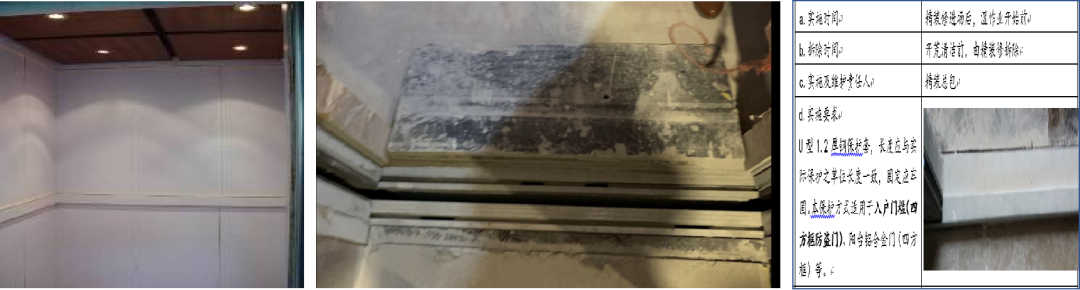
Elevator car protection / elevator door hole protection / threshold stone protection
Door cover, yang angle, stair protection:
9-centimeter wooden splint According to the size of the door cover to make a U-shaped protective case, firmly fixed around the door cover, height is not less than 1.2 meters, U-shaped flip width needs to cover the door cover.
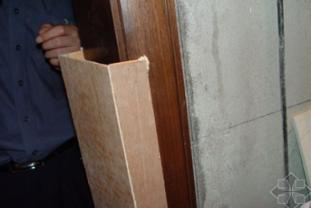
The finished yang angle guard angle is implemented yang angle guard angle, the angle height is not less than 1.2 meters, the width of the wings is not less than 30mm, the installation should be firm.
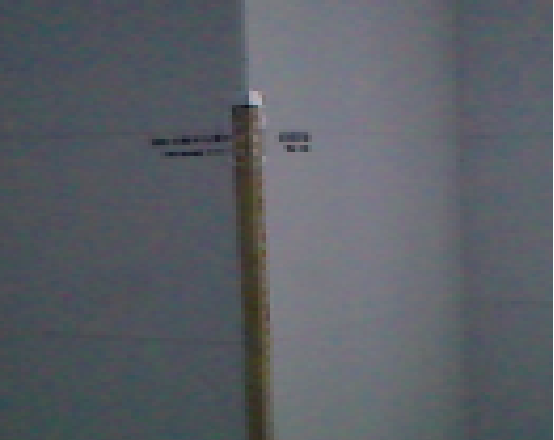
Protect the finished yang angle guard with a 9-centimeter splint or an L-shaped protective case with a 9-centimeter splint, and install securely.
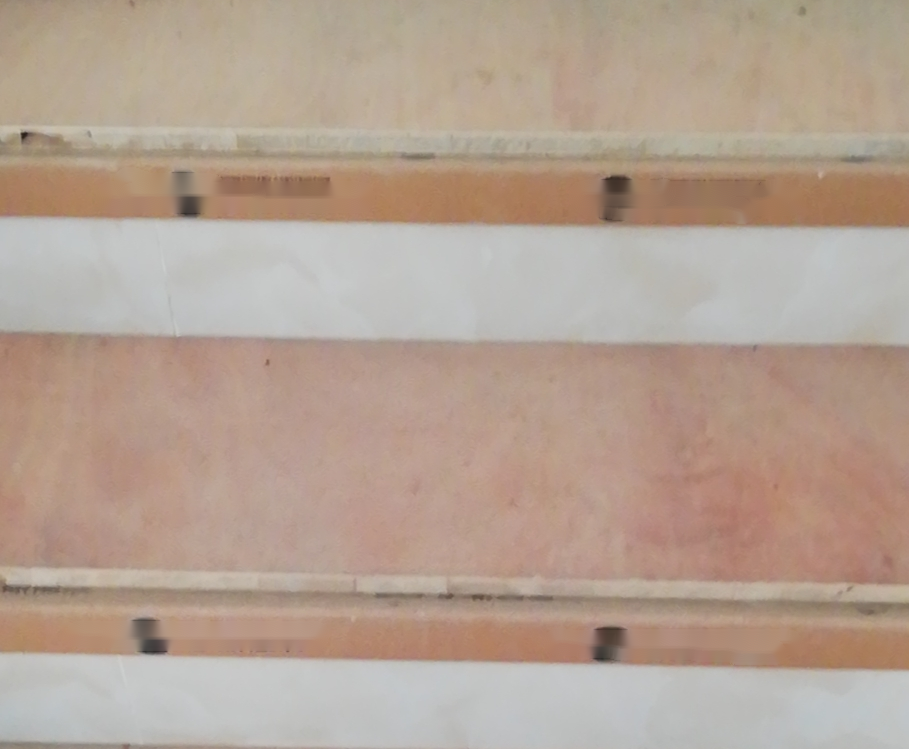
– Project construction process –
01
Prepare in advance
1.1
Construction deployment
On-site roads and the surrounding environment: construction can not affect the surrounding greening, not far from the residents of the construction pay attention to production noise, transportation.
Vertical transport: hardcover entry, the construction elevator has been removed, the indoor formal elevator has completed acceptance, hardcover units to do elevator car finished product protection, by the hardcover unit sent a person to open the elevator, as a vertical transport tool.
Construction organization: According to the actual situation on the site to prepare a practical construction organization design.
Coordinated management: coordination with construction units, supervision units, total package units, design units.
Bottom-of-the-deal learning: tender bottom, cost bottom, contract bottom, construction technology bottom, construction interface bottom, safety bottom, safety education and training, process training, and learning.
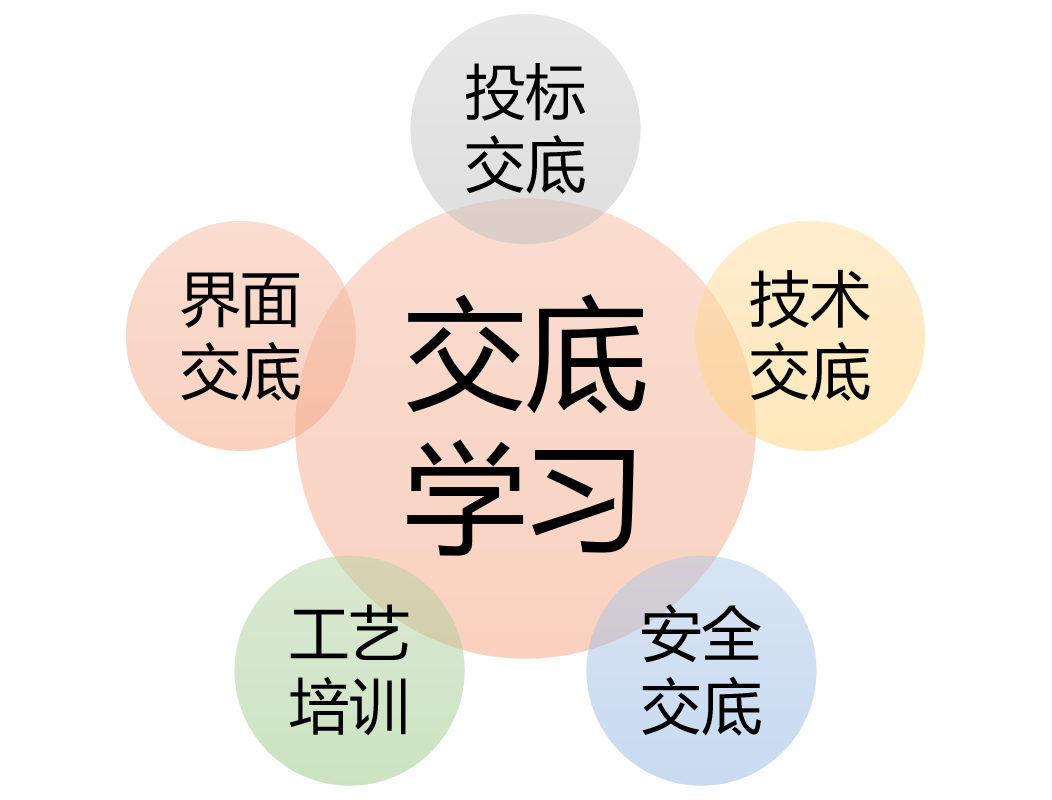
1.2
Construction organization
Project organization structure:
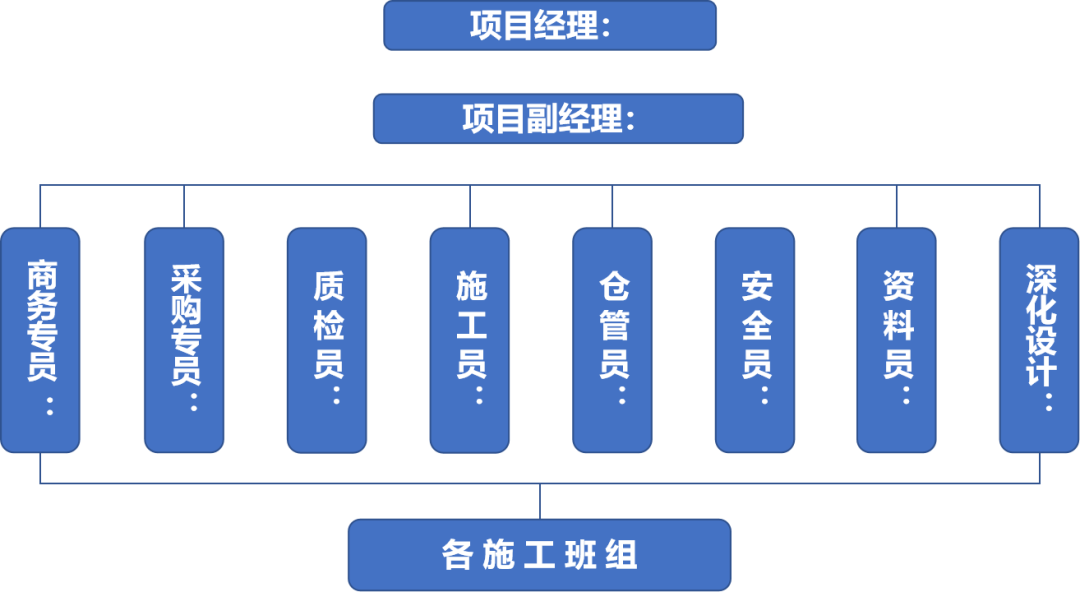
Team organization structure:
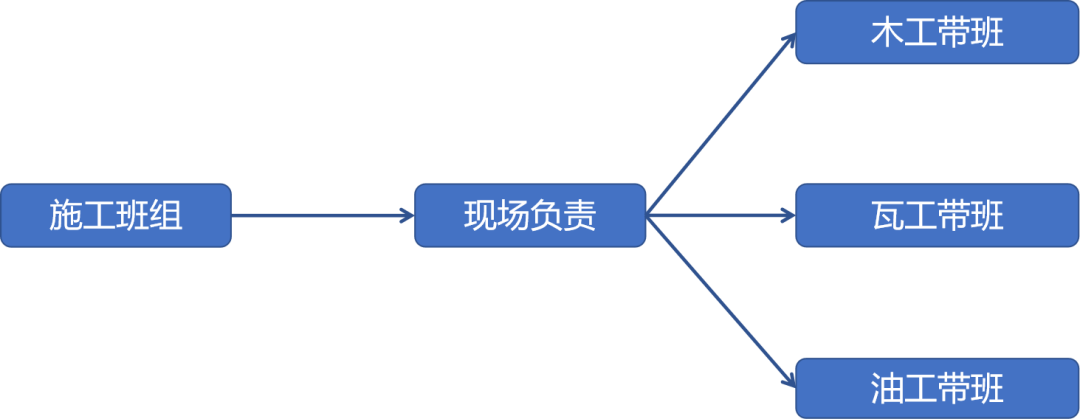
1.3
Material seal
Material seal:
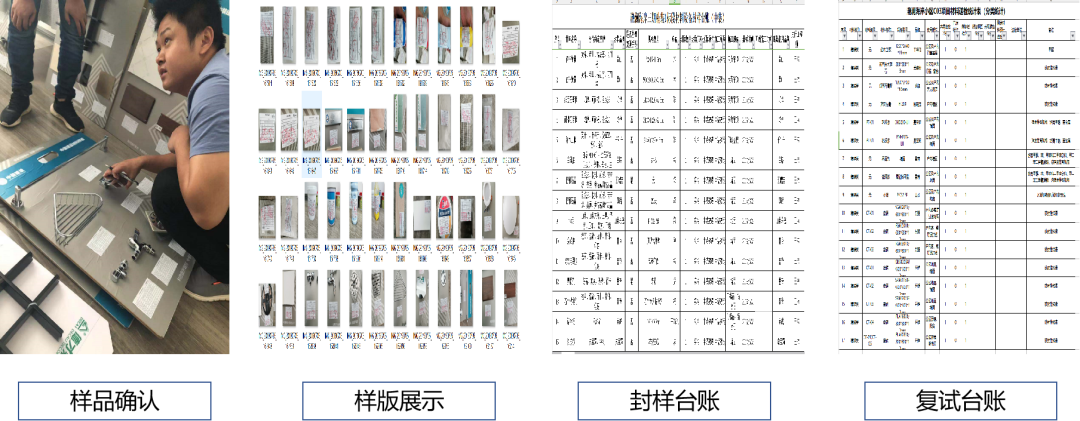
Time node: The starting time for sealing is to complete all material sealing work within 1 month of the entry of the total hardcover package, and this part of the sealing work serves as a model for hardcover solids and the basis for the implementation of bulk hardcover.
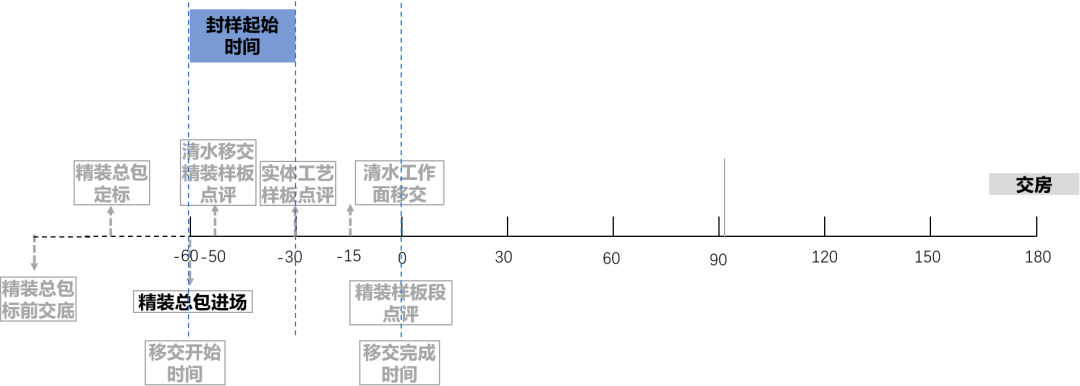
1.4
Design cross-base
Drawing triage:
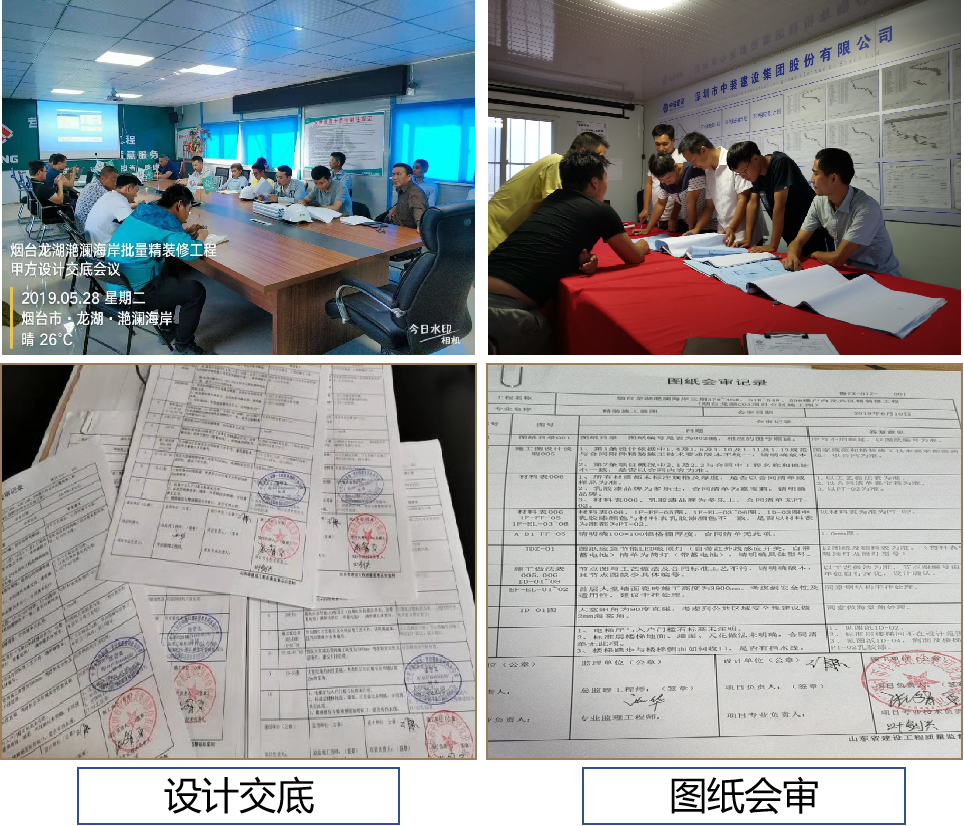
1.5
Line reviews
Construction line:
Step 1: The main control line, axis, finish surface control line (wheelbase minus 1m), the top surface around the wall is completed facing up to 250mm for the electromechanical elevation line, the ground 0.000 horizontal lines, each layer 1-meter horizontal line, line for the first step.
Step 2: The main control line of the total floor plan of each layer, the axis, the completion surface control line (wheelbase minus 1m), the top surface around the wall is completed facing up to 250mm for the electromechanical elevation line, the ground 0.000 horizontal lines, each layer 1-meter horizontal line, for the second step.
Step 3: According to the results of the straw line, for deepening After the designer partially adjusts the floor plan, but the modeling line, called the third step line.
Step 4: Take the middle control line of the walkway as the baseline, adjust the wall inside and outside the door cover related to the walkway to complete the face line fixed door cover, this line method is called the parallel line method for the fourth step line, also called the walkway construction method in the construction, the door cover finished construction method.
Step 5: In the production process, some of the original positioning lines will be covered by construction work, at this time the construction unit according to the original size in the same position re-placing lines, so-called the fifth step of the line, also known as the second line.
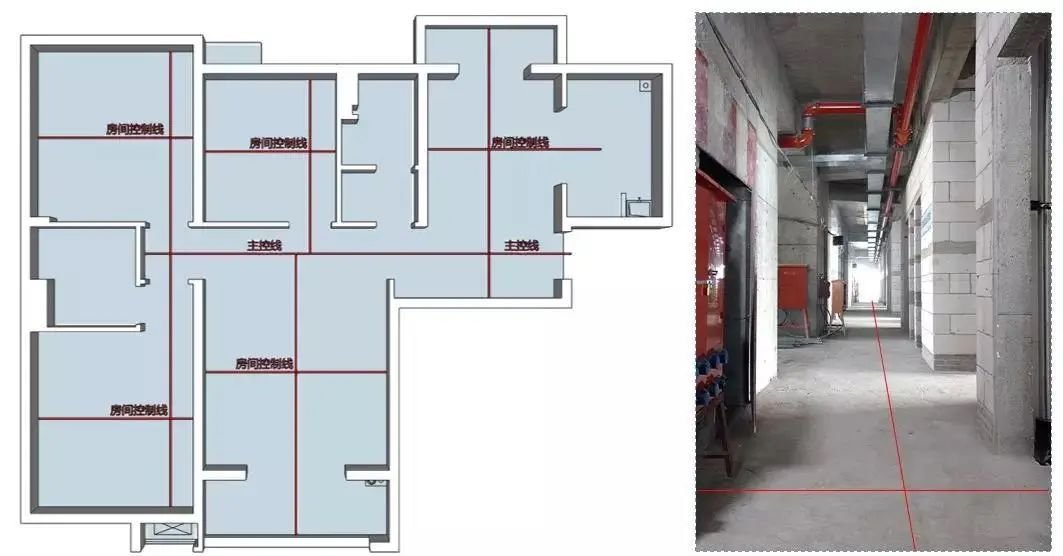
To ensure dimensional accuracy, on-site elevation control dimensions, are provided by us with the one-meter line, control line.
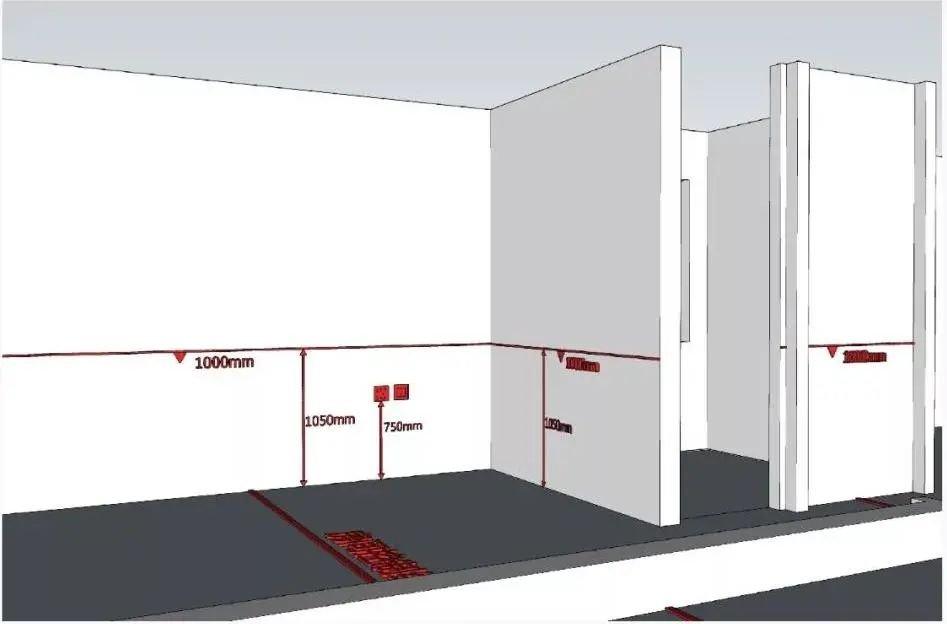
Detection method: carpet measurement using a two-meter ruler, at least cross-measuring at the same position, if a gap greater than 3mm or even 5mm appears under the ruler, indicating uneven ground.
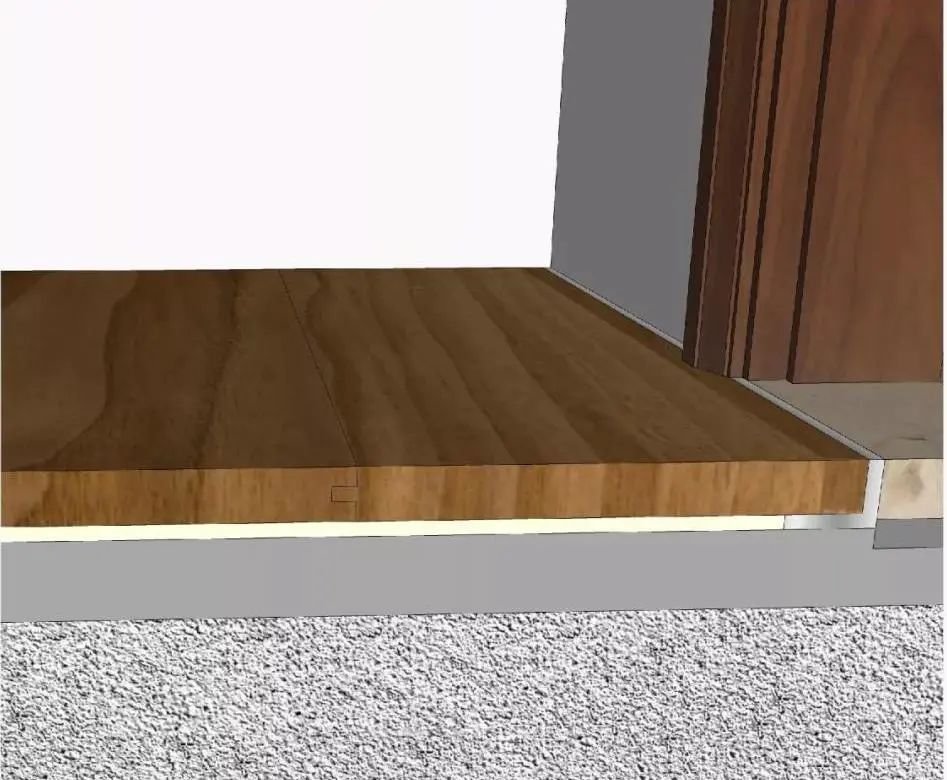
Sensors, showerheads and lamps must not be less than 300mm apart
Line management:
1, construction points: construction personnel in the construction, by the construction technical personnel on-site technical bottom, according to the construction blueprint design drawings with ink line ejected grass-roots, complete the surface line, by the project construction technical person in charge of the survey, before the construction, all dimensions of accuracy to the construction blueprint drawing design documents.
2, line project:
(1) The master and axis of the total plane of each layer
(2) Floor building elevation and surface finish face line
(3) Smallpox integrated cloth point
(4) The keel partition wall positioning line
(5) Door position line
(6) Top material split line
3, line requirements: the main control line of the total floor plan of each layer, axis, complete surface control line (wheelbase minus 1 meter), wall around the top surface to complete facing the ceiling elevation line, ground ± 0.000 Horizontal line, 1-meter horizontal line for each layer.
4, division of labor seed line: tiler painting finished face line (bathroom, kitchen, service room, latex paint, window cover line grass), oil workers painting finished face line (painting plaster), carpentry bullet completed Face (soft, hard, wood finishes).
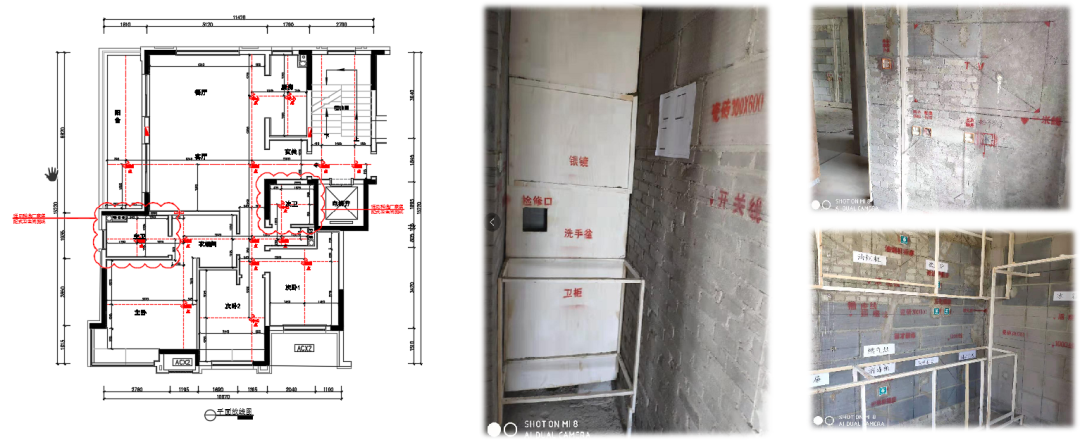
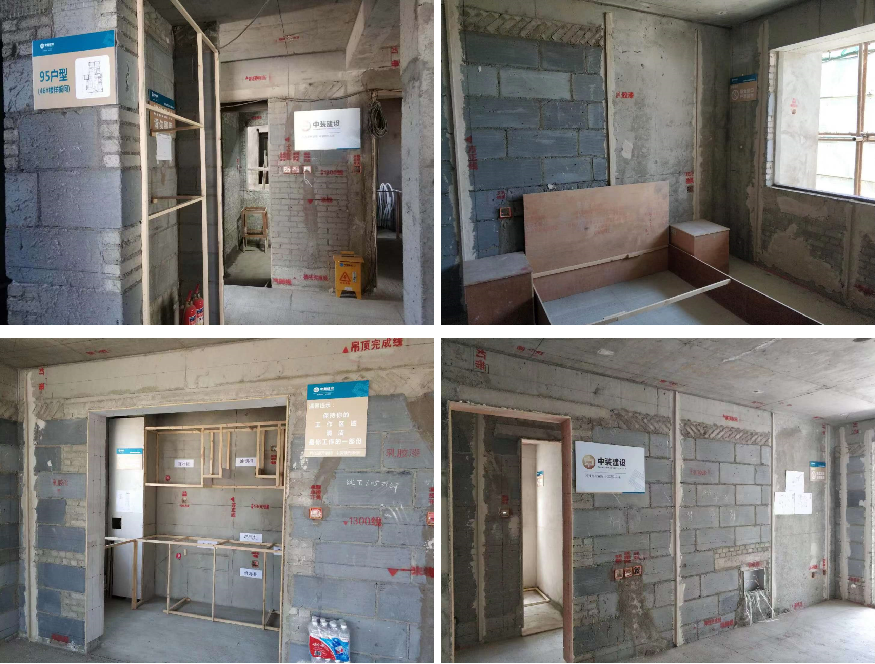
The cable-laying device:
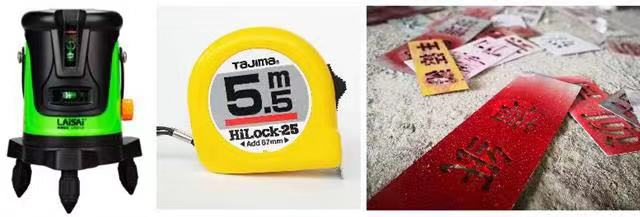